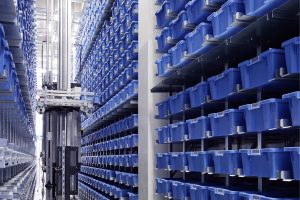
Ein softwaregesteuertes Transportgerät entnimmt Artikelbehälter aus einem Regalfach und führt sie der Person am Kommissionierplatz zu – ein automatisierter Vorgang, der viel Zeit einspart. Allerdings stellt sich Unternehmen die Frage, welche Lösung diese Aufgabe effektiver löst: Sollten sie lieber auf Regalbediengeräte oder doch eher auf eine Shuttle-Lösung setzen? Die Entscheidung ist abhängig von den individuellen Anforderungen.
Das Thema Kommissionierung ist in der Vergangenheit stets komplexer und kleinteiliger geworden. Die Gründe: die große Artikelvielfalt im gelagerten Sortiment und der Trend zu immer geringeren Bestellmengen. Das führt unter anderem auch zu immer mehr Laufwegen für die Mitarbeiter. Um diese zu verkürzen, empfiehlt es sich, ein automatisiertes Logistiksystem zu integrieren. Im Bereich der individuellen AKLs (AutoStore, Exotec & Co seien hier mal außen vorgelassen) müssen sich Unternehmen dabei zwischen zwei Lösungsansätze entscheiden: ein automatisiertes Kleinteilelager mit gassengebundenen Regalbediengeräten (RBG) oder ein Lager auf Shuttle-Basis. Beide Ansätze haben spezielle Vor- und Nachteile. Um für den eigenen Bedarf die beste Entscheidung zu treffen, sollten folgende Kriterien bedacht werden:
- Leistung
- Skalierbarkeit
- Verfügbarkeit
- Kosten
Shuttlelager – flexibel und leistungsstark
Im Vergleich zu klassisch RBG-betriebenen AKLs lassen sich Shuttlesysteme bei gleicher Stellplatzanzahl für höhere Leistungen konstruieren. Weiterhin lässt sich über die Anzahl der eingesetzten Shuttles die Leistung skalieren. Flexibel zeigen sich die Shuttle-Lager sowohl bei der Ausnutzung von Hallengeometrien wie auf bei der Umsetzung individueller Fahrstrategien. Durch den Einsatz von vielen Fahrzeugen des gleichen Typs entsteht dabei eine hohe Ausfalltoleranz. Nachteilig sind dagegen die höheren Kosten pro Stellplatz. Außerdem macht die hohe Anzahl der aktiven Komponenten das Gesamtsystem etwas störanfälliger und die Heber werden schnell zum limitierenden Faktor.
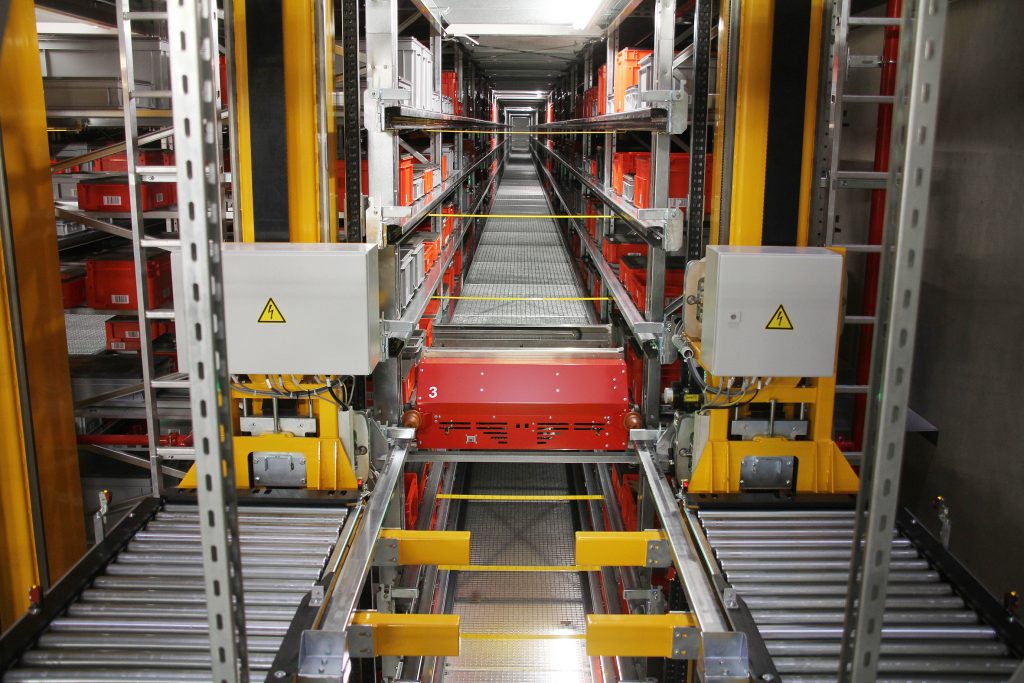
AKL mit RBG – zuverlässig und wartungsarm
Das klassische RBG-bediente AKL hat eine klar definierte Leistung: Ein Fahrzeug pro Gasse, welches alle horizontalen und vertikalen Bewegungen abbildet. Das führt zu einem zuverlässigen und wartungsarmen Betrieb. Pro Stellplatz entstehen geringere Kosten. Im Umkehrschluss besteht der Nachteil darin, dass im Falle eines Ausfalls des Gerätes die gesamte Gasse stillsteht. Zeitgleich lassen sich die Regalfächer im Gegensatz zu einem Shuttle-System nur schwer zu Fuß erreichen.
Einbindung in ein logistisches Gesamtkonzept
Das Kleinteilelager ist in der Regel Bestandteil eines logistischen Systems, bestehend aus Fördertechnik, Kommissionierung, Konsolidierung und Verpackung. Ob für das individuelle Gesamtkonzept ein Shuttle-System oder RBG bedientes AKL sinnvoller ist, sollte im Kontext der logistischen Anforderungen des Kunden betrachtet werden. Generalunternehmer wie Unitechnik Systems planen auf Basis vieler realisierter Projekte solche Gesamtsysteme und geben klare Empfehlungen, welches System für den individuellen Fall am geeignetsten ist.
Leave a Reply