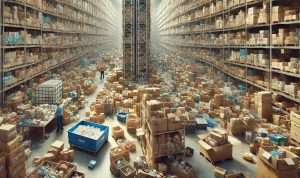
Unternehmen stehen heute vor der Herausforderung, Kosten zu senken, Prozesse zu vereinfachen und gleichzeitig nachhaltiger zu wirtschaften.
Die Verpackungsvielfalt ist hierbei ein zentraler Ansatzpunkt: Weniger Varianten bedeuten geringere Produktions- und Lagerkosten, effizientere Prozesse und eine geringere Umweltbelastung.
Dieser Beitrag beleuchtet sechs wesentliche Schritte, um Verpackungssortimente zu optimieren und langfristig Wettbewerbsvorteile zu schaffen.
1. Analyse des aktuellen Verpackungssortiments
Die Grundlage jeder Optimierung liegt in der umfassenden Analyse des bestehenden Verpackungssortiments. Dieser Prozess beginnt mit der Erhebung von Daten über alle bestehenden Verpackungsvarianten und deren Produktverknüpfungen. Dazu zählen Informationen über Konstruktionen, Materialien und Größen.
Schlüsselaspekte:
- Erfassen aller Varianten: Es ist entscheidend, dass die Verpackungsstammdaten alle relevanten Verpackungsinformationen enthalten. Dazu gehören Konstruktion, Materialien und Größen, sowie Verbrauchsdaten, Lagerbestände und Kosten pro Verpackungstyp
- Bewertung der Varianten: Jede Verpackung sollte hinsichtlich ihrer Funktionalität, Kosten, Produktverknüpfung und Bedeutung für den Kunden bewertet werden.
- Identifikation von Schwachstellen: Redundante Verpackungen, ineffiziente Konstruktionen,
“ähnliche” Größen oder ein geringer Volumennutzungsgrad sollten gezielt analysiert werden.
Die Ergebnisse dieser Analyse dienen als Basis für alle weiteren Schritte und definieren die Schwerpunkte der Optimierung.
2. Bewertung und Priorisierung
Nicht alle Verpackungsvarianten haben den gleichen Stellenwert. Daher müssen Unternehmen bewerten, welche Verpackungen wirklich notwendig sind und welche eliminiert werden können.
Ansätze zur Priorisierung:
- Kundenorientierung: Kundenspezifische Verpackungen müssen gesondert betrachtet werden, da Sie an die Freigabe des Kunden gebunden sind
- Materialeffizienz: Verpackungen mit hohem Materialverbrauch oder schlechter Recyclingfähigkeit sollten überprüft und ersetzt werden.
- Eliminierung redundanter Varianten: Verpackungen, die ähnliche Funktionen erfüllen und/oder “ähnliche” Größen aufweisen, können für eine Konsolidierung detaillierter betrachtet werden.
Die Priorisierung sorgt dafür, dass nur so viel Verpackungsmaterialien wie notwendig eingesetzt werden und die Verpackungsvielfalt wesentlich reduziert werden kann.
3. Entwicklung neuer Verpackungsstandards
Nach der Bewertung und Priorisierung ist die Entwicklung von Standards der nächste logische Schritt. Standards schaffen Klarheit und Effizienz, indem sie die Vielfalt reduzieren und Prozesse vereinfachen.
Wichtige Aspekte:
- Materialoptimierung: Nachhaltige und kosteneffiziente Materialien sollten bevorzugt eingesetzt werden.
- Einheitliche Konstruktionen: Flexible Konstruktionen und die Festlegung geeigneter Größencluster verringern Komplexität und Kosten.
- Handling: Verpackungen sollten so gestaltet sein, dass sie optimal auf die Packprozesse und Logistikanforderungen angepasst sind.
Diese Standards tragen zur Reduktion der Beschaffungs-, Produktions- und Lagerhaltungskosten bei und verbessern die Prozesseffizienz.
4. Implementierung
Die Implementierung der neuen Verpackungsstandards stellt sicher, dass die definierten Verbesserungen in der Praxis angewandt werden. Dieser Schritt erfordert eine enge Zusammenarbeit zwischen verschiedenen Abteilungen.
Schritte zur Umsetzung:
- Prüfen der Umsetzbarkeit: Die neuen Standards sollten hinsichtlich ihrer Integration in bestehende Produktions- und Logistikprozesse getestet werden.
- Optimierung der Beschaffung: Einheitliche Standards und aktuelle Spezifikationen je Verpackung helfen, Materialien kostengünstiger und effizienter auszuschreiben und zu beschaffen.
- Automatisierung: Wo möglich, sollten Verpackungsprozesse durch den Einsatz moderner Technologien automatisiert werden.
Eine gut geplante Implementierung minimiert Störungen und maximiert die Effizienz.
5. Kommunikation und Change-Management
Der Erfolg jeder Veränderung hängt von der Akzeptanz der beteiligten Personen ab. Daher ist eine klare und transparente Kommunikation unabdingbar.
Maßnahmen zur Unterstützung des Wandels:
- Stakeholder einbinden: Informieren Sie interne und externe Partner über die Vorteile der neuen Standards.
- Schulungen: Teams müssen geschult werden, um die neuen Prozesse effizient umsetzen zu können.
- Feedbackmechanismen: Rückmeldungen von Mitarbeitern und Partnern helfen, potenzielle Probleme frühzeitig zu erkennen und zu beheben.
Ein professionelles Change-Management sorgt für eine reibungslose Einführung und Akzeptanz der neuen Verpackungsstrategie.
6. Überwachung und Optimierung
Die Einführung neuer Standards ist kein einmaliger Prozess. Kontinuierliche Überwachung und Verbesserung sind entscheidend, um langfristigen Erfolg sicherzustellen.
Best Practices:
- Ergebnisanalyse: Regelmäßige Überprüfung von KPIs wie Kostenersparnis, Effizienzsteigerungen und Kundenzufriedenheit.
- Anpassungsfähigkeit: Flexibel auf Veränderungen im Markt oder neue Technologien reagieren.
- Innovationsförderung: Fortlaufende Suche nach neuen Materialien und Prozessen, die die Verpackungsstrategie weiter verbessern.
Ein systematisches Monitoring stellt sicher, dass die Verpackungsstrategie stets auf dem neuesten Stand bleibt und den Unternehmenszielen entspricht.
Fazit
Die Reduzierung der Verpackungsvielfalt ist eine effektive Methode, um Kosteneinsparungen zu erzielen, die Komplexität in der Beschaffung, Produktion und Logistik zu reduzieren und die Prozesseffizienz nachhaltig zu steigern. Die sechs beschriebenen Schritte bieten Unternehmen einen praxistauglichen Ansatz, um diese Ziele zu erreichen. Durch eine detaillierte Analyse, klare Priorisierung und Standardisierung, sorgfältige Implementierung sowie kontinuierliches Monitoring können signifikante Verbesserungen erzielt werden. Dies führt nicht nur zu finanziellen Vorteilen, sondern stärkt auch die Wettbewerbsfähigkeit und unterstützt die Nachhaltigkeitsziele des Unternehmens.
(Bild KI generiert)
Leave a Reply