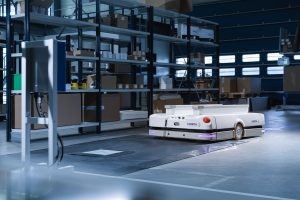
Ob als automatisierte Gabelstapler, Unterfahrschlepper oder in Kombination mit Hubeinheiten – die Automatisierung innerbetrieblicher Materialflüsse mit Fahrerlosen Transportsystemen (FTS/AGV) ist eines der Topthemen der Intralogistik.
Die Vorteile der FTS liegen auf der Hand:
- Sie sind flexibel,
- lassen sich perfekt in bestehende Strukturen integrieren,
- entlasten die Mitarbeiter und
- sind nahezu unterbrechungsfrei einsetzbar.
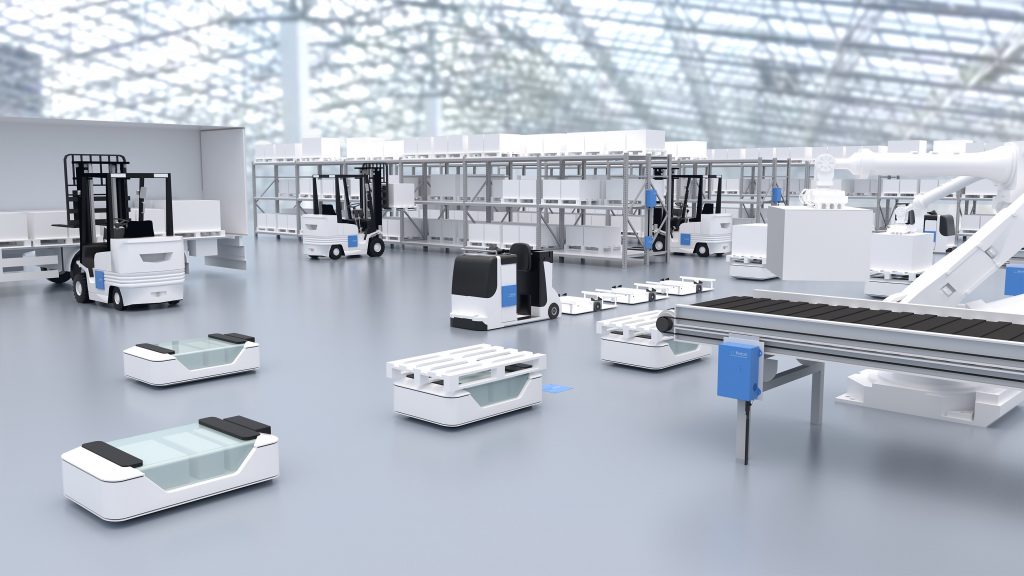
Um eine maximale Prozesseffizienz zu erreichen, müssen die Fahrzeuge dauerhaft zur Verfügung stehen. Allerdings ist die Energieversorgung der Flaschenhals, für einen vollautomatisierten Betrieb. Induktive Ladesystemesind hierfür eine zukunftsfähige Alternative.
Nachteile von Ladekonzepten mit Steck- und Schleifverbindungen
Bisher werden FTS häufig über konventionelle Ladekontakte mit Steck- oder Schleifverbindungen geladen. Die Energieübertragung findet dabei meist in längeren Pausen oder nach Schichtende statt. Hierdurch fällt das Energielevel der Batterien im Betrieb kontinuierlich ab und muss durch längere Ladephasen ausgeglichen werden.
Da die Batterien nicht kontinuierlich zwischengeladen werden, müssen sie deutlich größer ausfallen und höhere Kapazitäten haben als eigentlich nötig. Erfolgt das Aufladen der gesamten Fahrzeugflotte nach Schichtende, steigen der Energieverbrauch und die damit verbundenen Kosten rapide an. Zum Aufladen sind spezielle Wartezonen notwendig. Diese befinden sich aus Arbeitsschutzgründen nicht in der Nähe der Produktionsbereiche, sondern weiter entfernt. Wenn die fahrerlosen Transportfahrzeuge während der Fertigung zu den eingerichteten Ladestationen fahren, fehlen sie im Produktionsprozess.
Erfolgt die Aufladung über Schleifverbindungen, sind eine aufwendige Beschaltung und eine Absenkkinematik erforderlich, um die Kontakte nur zum Ladezeitpunkt zu aktivieren. Die Lösungen sind relativ teuer, unflexibel, störanfällig und erfordern bauliche Eingriffe in die Infrastruktur.
Leitliniensysteme: induktiv, aber teuer und unflexibel
Beim Einsatz von FTS in Leitliniensystemen folgen die Fahrzeuge einer festgelegten Spur. Das Laden erfolgt induktiv; allerdings sind umfangreiche Eingriffe in die Infrastruktur nötig, um die Leiter im Boden zu installieren. Die Fahrstrecke muss dauerhaft mit Energie versorgt werden. Das System ist sehr kosten- und wartungsintensiv.
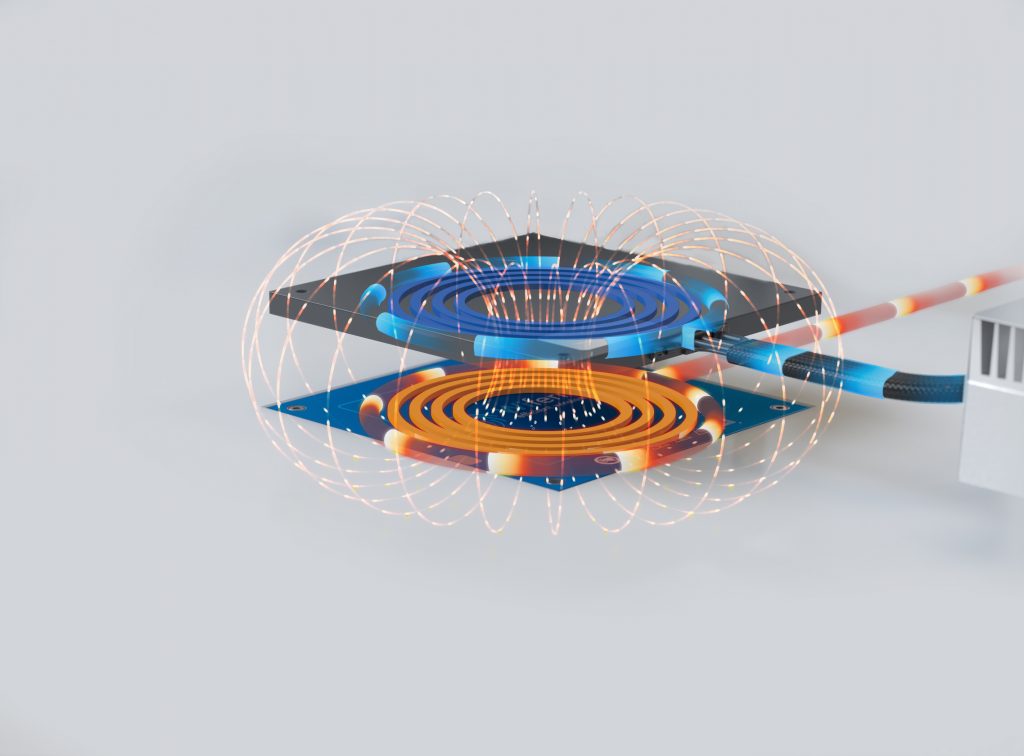
„In-Process-Charging“ ermöglicht vollautomatisierte Arbeitsabläufe
Intelligente Punktladesysteme mit einer berührungslosen Energieübertragung zum Aufladen der Lithium-Ionen-Batterien bieten zahlreiche technische und wirtschaftliche Vorteile. Die Systeme bestehen aus einer stationären Sendeeinheit und fahrzeugseitig aus einer Empfangselektronik. Die patentierte Ladetechnologie umfasst eine Wallbox und ein Ladepad. Im Fahrelosen Transportsystem wird die Empfangselektronik mit Empfängerspule, mobiler Ladeeinheit und Energiespeicher verbaut. Innerhalb einer Sekunde nachdem die Fahrzeuge das Ladepad erreicht haben, beginnt der Ladeprozess vollautomatisch. Dieses „In-Process-Charging“ eröffnet völlig neue Automations- und Produktionskonzepte. Die Sendeeinheit lässt sich schnell und einfach an neuralgischen Punkten im Lager installieren, beispielsweise auf häufig frequentierten Fahrwegen oder an Be- und Entladestationen. So können selbst kürzeste Standzeiten für das Laden genutzt werden. Arbeitsabläufe müssen nicht mehr durch Ladevorgänge unterbrochen werden und lange Ladepausen entfallen. Damit erhöht sich die Verfügbarkeit um bis zu 30 % und die FTS können ihre Aufgaben im 24/7-Betrieb erledigen. Ändern sich Abläufe oder andere Anforderungen, lässt sich das System schnell anpassen und komfortabel an neuen Stellen positionieren.
Im Ergebnis erfüllt das prozessparallele Laden die Anforderungen an eine vollautomatisierte, wartungsfreie Energieversorgung und könnte schon bald den derzeitigen Ladestandard in der Intralogistik ersetzen.
Weitere Informationen zum induktiven Laden von FTS erhalten Sie unter www.wiferion.com
Leave a Reply